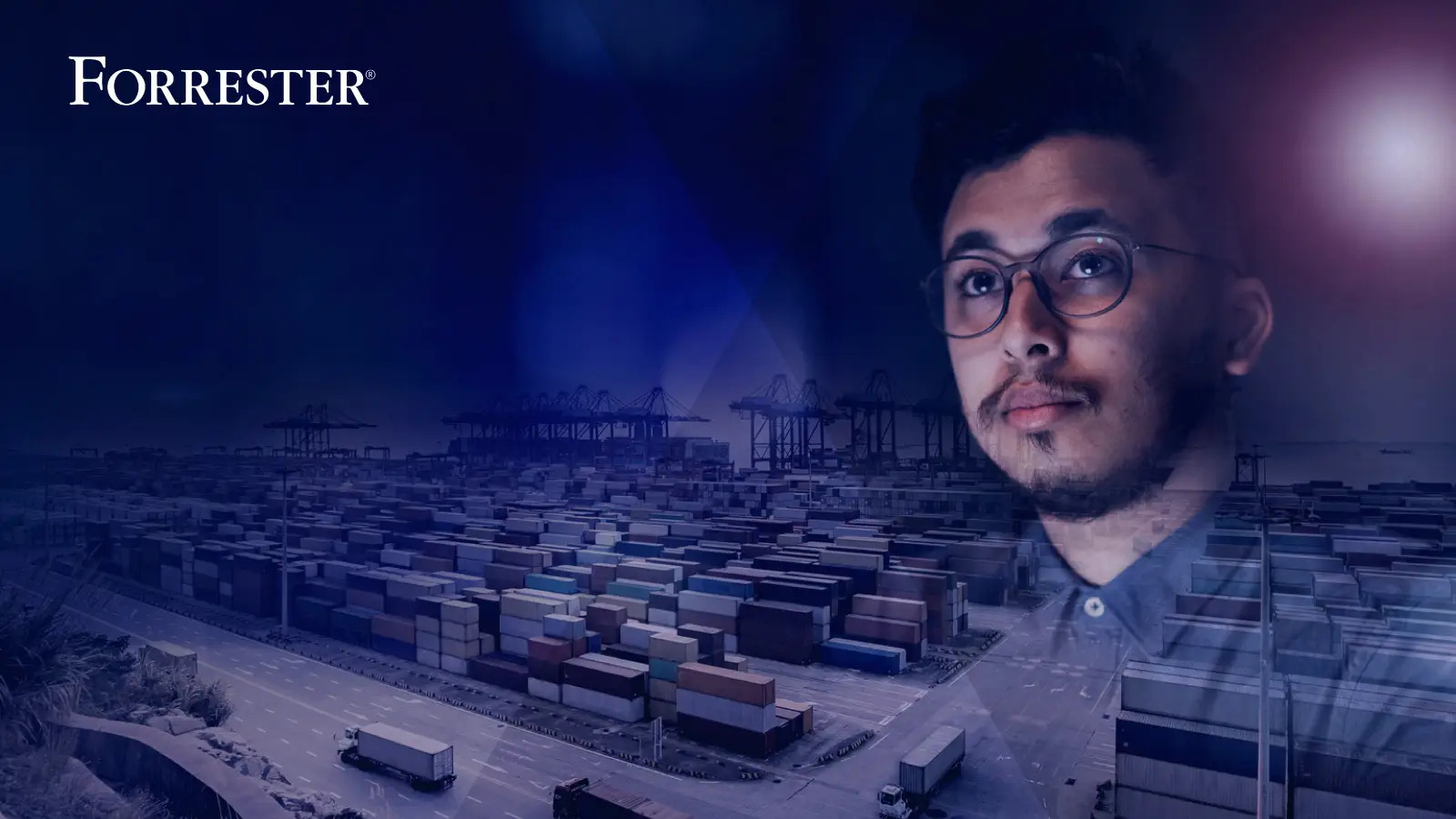
阅读新的Forrester报告:Anaplan的总体经济影响™
第三方研究发现,在3年的时间内,多个客户组合的投资回报率为303%
总部位于东京的全球化学品公司Denka开始可视化和同步其端到端供应链规划过程。一个新的解决方案建立在anplan平台上,将需求计划、库存计划、生产计划和损益(P&L)模拟连接起来。因此,Denka在多个站点实现了更大的业务协作,决策敏捷性和整体公司盈利能力。
anplan已经并将继续为我们的运营带来重大改进。Kazuya Tokumoto,董事总经理
业务决策,因为整个端到端供应链的计划都是实时集成和重新计算的。
产品和等级方差分析的下钻报告有助于确定方差的根本原因。
协作,多个操作和函数共享相同的数据源进行规划。
Denka如何通过与德勤的合作,将整合的商业规划与Anaplan结合起来。
Our ultimate goal is to establish an autonomous supply network that has minimal human interaction by leveraging cutting-edge digital technology. This will be achieved through the following steps:
\r\n(1) Achieving a visualization of our end-to-end supply chain.
\r\n(2) Creating greater business collaboration with partners.
\r\n(3) Optimizing our transportation network and inventory.
\r\n(4) Using AI to help predict future events.
\r\nAnd finally, establish an automated operations driving mechanism that enables autonomous decision-making without human intervention.
\r\nAs a first step, we’re focusing on planning operations — achieving insight into our supply chain. We realized synchronized planning and fulfillment is vital here. We needed extensive visibility into the supply chain and to balance supply and demand in real time to make better strategic decisions.
\r\nSo how do we achieve synchronized planning and fulfillment? We’ve introduced an integrated business planning process consisting of four areas:
\r\n(1) Demand Planning to clarify how much demand we have from each customer;
\r\n(2) Inventory Planning to find which product or grade inventory should be set up;
\r\n(3) Production Planning to discover what should be produced in what order; and finally
\r\n(4) P&L simulation to see how much profit could be achieved when the plan is changed.
\r\nThen we choose a best-in-class tool to help us: real-time cloud planning platform Anaplan. Anaplan is a connected planning tool that is flexible and secure. It has three key features that help our project:
\r\n(1) Access from anywhere: Being cloud-based, we can stay connected anywhere, and on any device to accelerate our business decisions. Even in the event of an emergency such as COVID-19, we can carry out your work from home.
\r\n(2) Collaborative planning: The planning data within Anaplan is all connected. For example, if a salesperson changes the Demand Plan, the system automatically suggests a new production plan to meet demand. It then calculates the right amount of raw material required and checks the projected inventory in real time. This means we can do collaborative planning, rather than sequential planning, shortening the overall planning cycle time.
\r\n(3) Multi-scenario planning: With all the demand, production, and inventory planning data connected through Anaplan, our planners can see accurate P&L impact. We can use this for scenario planning to maximize profits and slice and dice the data for further customer and profitability analysis.
\r\nWe’re already reaping the rewards from Anaplan.
\r\n(1) Visualized end-to-end planning: All plans across the end-to-end supply chain are integrated and recalculated on the fly, enabling faster decision-making. From demand through procurement, the integrated plan is visible from a birds-eye view to encourage holistic, optimized decisions.
\r\n(2) Changing mindsets. By lifting barriers between departments, each planner understands how their own work impacts others’. With newfound perspective, planners can more effectively collaborate across functions and tackle end-to-end issues.
\r\n(3) Free from routine work. Planners are free from manually merging data from various sources. Everything is in Anaplan. Instead of spending time on low-impact tasks, planners can refocus their efforts and contribute to more analytical and strategic work.
\r\n(4) Accelerated variance analysis. Determining planning accuracy is no longer a complex operation. Automatically generated reports allow drill-down of variance analysis to the product and grade level. Identifying the root cause of variances is faster than ever before.
\r\nI’d now like to show you some videos of interviews of our teams telling you the benefits they’ve already seen.
\r\nText: “What are the benefits of implementing Anaplan into your operations?”
\r\nKazuya Tokumoto, Managing Director (speaking Japanese): We started discussing with everyone in charge of our plants, sales, and engineering departments to identify the needs of our system. Then at the designing phase of Anaplan, each department’s data analysis and what the teams should do, what they could not do, whether they wanted to do it but could not do it. All these issues have become clearer.
\r\nThis made it possible for us to analyze our operations. Then we have realized that we need to run a full check of these operations’ analyses, not just in the areas related to Anaplan, but to the overall operations.
\r\nI believe this is all thanks to Anaplan. As such, we can say that Anaplan not only gave us an application system, but it also made us realis important things. That is to say, Anaplan was both an excellent instructor and a great teacher to us.
\r\nAnd the most important point of all, is that Anaplan projects brought out from each staff member, especially younger ones, capabilities, motivation, and out-of-the-box ways of thinking. I believe this has resulted in, and will continue to result in, important improvements to our operations.
\r\nYuki Shintani, Sales Leader (speaking Japanese): It is all about real-time structure of planning operations. We are a manufacturing company, so we purchase raw materials and manufacture products in the manufacturing department. Then we ship these products to sell to our customers overseas.
\r\nBefore, these operations were managed by each department. Persons in charge created and processed data manually in Excel files. Then we discussed about the data in these files over the phone or by email, so it was like a human chain operation.
\r\nBut after we deployed Anaplan, these planning operations, these tasks that we used to do with Excel, are all processed in Anaplan. So now everyone can visualize the data simultaneously in real-time.
\r\nI believe that we now have a system in which the sales forecast increases, this information can be flawlessly communicated to the manufacturing department and the raw material purchasing department.
\r\nCindy Lee, Group Supply Chain General Manager: Anaplan is a single platform that allows all the functions to work together. It’s like a single source of information for us to have the updated supply and demand situation so that we, any changes, we are able to act quickly to bring the materials on time for the customers.
\r\nSo that actually streamlined communication because, I mean, streamlined communication is having to do with teams, and having to pick up the phone, whether you actually come to a (unintelligible) in this communication.
\r\nSo that single database will help us. Every stakeholder will have the latest information to manage the supply and demand situation. Especially our [unintelligible] or the telemarketers is one.
\r\nHui Peng Leang, Head of In-Plant Logistics: We can use anywhere for this Anaplan, even at home. And because this [is] an app, so we can download it phone site. And especially I’m the one to check the MMP. So if MMP is maybe less, I can highlight immediately in the sales side. So this is quite nice for us.
\r\nAnd also we have communication with all the salespersons, because of our sales, most of the sales [are] in China and Europe. So we can get them together, to work off this function and to achieve cost to serve. For reduced order of cost, [to] achieve order operation.
\r\n"}}" id="text-b70894489e" class="cmp-text">你好。今天,我们将探讨我们在Denka Seraya工厂成功的综合业务规划项目。
我们的最终目标是利用尖端的数字技术,建立一个人机交互最少的自主供应网络。这将通过以下步骤实现:
(1)实现我们端到端的供应链可视化。
(2)加强与合作伙伴的业务协作。
(3)优化运输网络和库存。
(4)利用人工智能帮助预测未来事件。
最后,建立自动运营驱动机制,实现无人干预的自主决策。
作为第一步,我们专注于规划运营——实现对供应链的洞察。我们意识到同步计划和实现在这里是至关重要的。我们需要广泛地了解供应链,实时平衡供应和需求,以便做出更好的战略决策。
那么,我们如何实现同步的计划和实现呢?我们引入了一个集成的业务规划流程,包括四个方面:
(1)需求计划,明确每个客户对我们有多少需求;
(2)库存计划,确定应该建立哪个产品或等级的库存;
(3)生产计划,发现什么应该按什么顺序生产;最后
(4)模拟损益,看看改变计划后能获得多少利润。
然后我们选择了一个一流的工具来帮助我们:实时云规划平台Anaplan。Anaplan是一个灵活、安全的连接规划工具。它有三个关键特性可以帮助我们的项目:
(1)从任何地方访问:基于云计算,我们可以在任何地方和任何设备上保持连接,以加速我们的业务决策。即使遇到COVID-19等紧急情况,我们也可以在家开展工作。
(2)协同规划:Anaplan内部的规划数据都是连通的。例如,如果销售人员更改了需求计划,系统会自动建议新的生产计划来满足需求。然后计算所需原材料的正确数量,并实时检查预计库存。这意味着我们可以进行协同规划,而不是顺序规划,缩短整体规划周期时间。
(3)多场景规划:通过Anaplan将所有需求、生产和库存规划数据连接起来,我们的规划人员可以看到准确的损益影响。我们可以将此用于场景规划,以实现利润最大化,并将数据切片,用于进一步的客户和盈利能力分析。
我们已经从Anaplan获得了回报。
(1)可视化的端到端规划:端到端供应链上的所有计划都被集成并实时重新计算,从而实现更快的决策。从需求到采购,从鸟瞰的角度来看,综合计划是可见的,以鼓励整体的,优化的决策。
(2)改变心态。通过消除部门之间的障碍,每个规划者都了解自己的工作如何影响他人的工作。有了新的视角,规划人员可以更有效地跨职能协作,解决端到端问题。
(3)不从事日常工作。规划者无需手动合并来自各种来源的数据。一切都在阿纳普里。与其把时间花在低影响的任务上,规划者可以重新集中精力,致力于更具分析性和战略性的工作。
(4)加速方差分析。确定规划的准确性不再是一个复杂的操作。自动生成的报告允许向下钻取差异分析到产品和等级级别。确定差异的根本原因比以往任何时候都要快。
现在我想给你们看一些我们团队的面试视频,告诉你们他们已经看到的好处。
文本:“在你的运营中实施Anaplan有什么好处?”
Kazuya Tokumoto,董事总经理(说日语):我们开始与负责工厂、销售和工程部门的每个人讨论,以确定我们系统的需求。然后在ananplan的设计阶段,每个部门的数据分析以及团队应该做什么,他们不能做什么,他们是否想做但不能做。所有这些问题都变得更加清晰。
这使我们能够分析我们的操作。然后我们意识到我们需要对这些操作的分析进行全面检查,不仅仅是在与Anaplan相关的领域,而是对整个操作进行检查。
我相信这都要感谢Anaplan。因此,我们可以说,anplan不仅给了我们一个应用系统,而且它也让我们实现了一些重要的事情。也就是说,anplan对我们来说既是一个优秀的导师,也是一个伟大的老师。
最重要的一点是,Anaplan项目激发了每个员工,尤其是年轻员工的能力、动力和创新的思维方式。我相信这已经导致,并将继续导致,我们的业务的重要改进。
Yuki Shintani,销售主管(说日语):这都是关于计划运作的实时结构。我们是一家制造公司,所以我们在制造部门采购原材料和制造产品。然后我们把这些产品运到海外销售给我们的客户。
在此之前,这些业务由各个部门管理。负责人在Excel文件中手工创建和处理数据。然后我们通过电话或电子邮件讨论这些文件中的数据,所以这就像一个人链操作。
但是在我们部署了Anaplan之后,这些计划操作,这些我们用Excel完成的任务,都在Anaplan中处理。所以现在每个人都可以同时实时地可视化数据。
我相信我们现在有一个销售预测增加的系统,这个信息可以完美地传达给生产部门和原材料采购部门。
集团供应链总经理李欣欣:anplan是一个允许所有功能一起工作的单一平台。对于我们来说,这就像一个单一的信息来源,可以了解最新的供需情况,这样我们就可以迅速采取行动,及时为客户提供材料。
所以这实际上简化了沟通,因为,我的意思是,简化沟通是与团队有关的,必须拿起电话,无论你是否真的在沟通中(听不清)。
所以这个单一的数据库会帮助我们。每个利益相关者都将拥有最新的信息来管理供需状况。特别是我们的(听不清)或者电话推销员是其中之一。
梁惠鹏,厂内物流主管:我们可以在任何地方使用这个ananplan,甚至在家里。因为这是一个应用程序,所以我们可以从手机网站下载它。尤其是我是检查MMP的人。所以如果MMP可能更少,我可以立即在销售方面突出显示。这对我们来说很好。
而且我们和所有的销售人员都有沟通,因为我们的销售大部分是在中国和欧洲。所以我们可以把它们放在一起,消除这个功能,实现服务成本。为降低订单成本,实现订单操作。