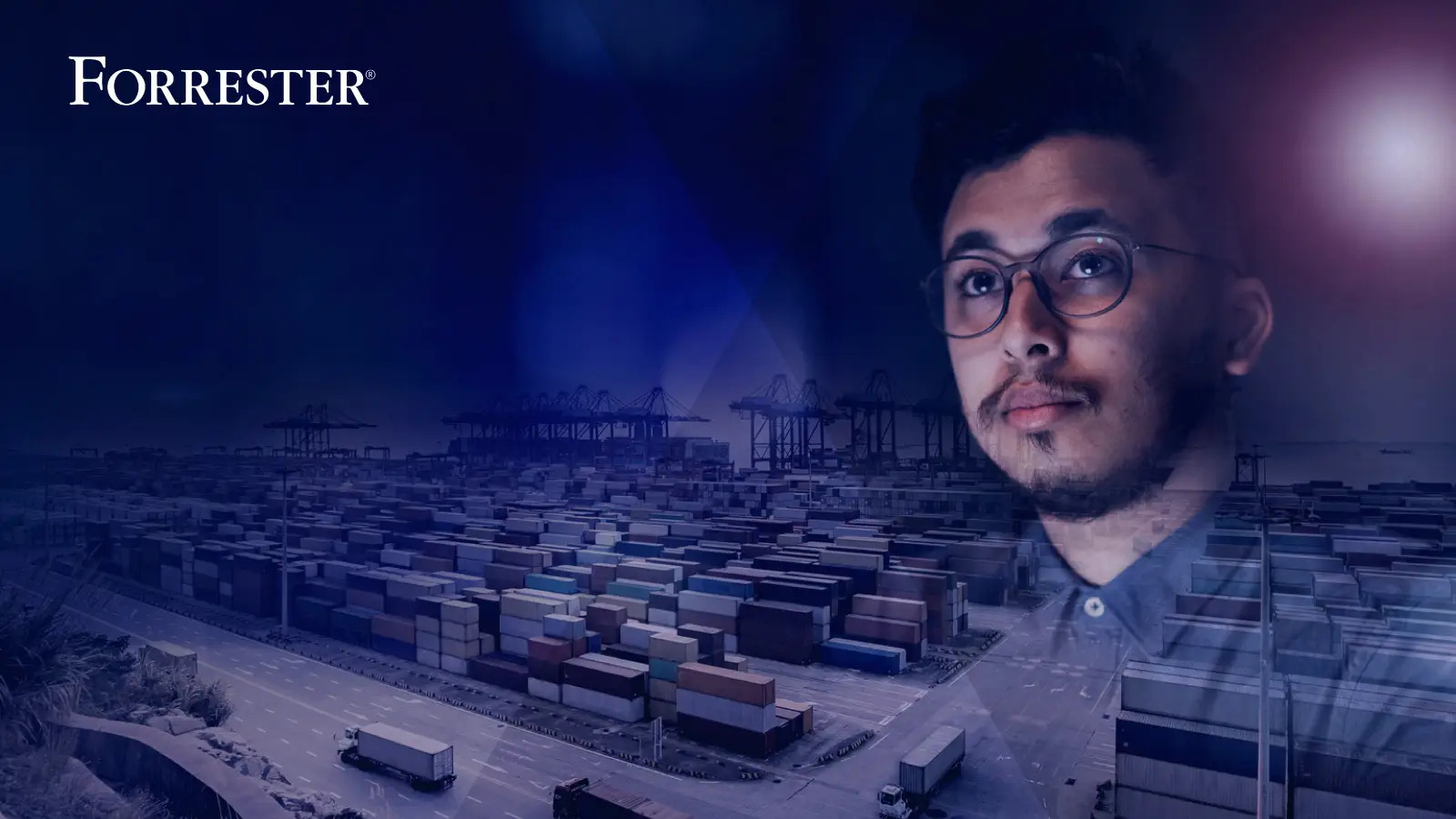
阅读新的Forrester报告:Anaplan的总体经济影响™
第三方研究发现,在3年的时间内,多个客户组合的投资回报率为303%
过去,我们需要5天时间来对需求变化做出反应。现在,使用Anaplan,我们只需不到五分钟就能在生产中提出必要的调整。RK Del Rosario,供应链计划经理
全球菠萝产量
Prior to Anaplan, Del Monte Pacific Ltd. was using a mix of hundreds of large spreadsheets and inflexible legacy tools to manage their supply chain process and financial planning. The process was slow—even simple scenarios required up to six hours to run. In order to avoid the inflexibility and delays of using the legacy tool, averages were used for many planning scenarios, leading to large discrepancies between forecasts and actual costs. Inventory management was disjointed, and when there was misalignment in the planning process, it led to lost sales opportunities and excess inventories.
\r\n\r\n"}}" id="text-e9cf742782" class="cmp-text">
在ananplan之前,德尔蒙特太平洋有限公司使用数百个大型电子表格和灵活的遗留工具来管理他们的供应链流程和财务规划。这个过程很慢,即使是简单的场景也需要长达6个小时才能运行。为了避免使用遗留工具的不灵活性和延迟,在许多规划方案中使用平均值,导致预测和实际成本之间存在很大差异。库存管理是脱节的,当计划过程中出现偏差时,就会导致销售机会的丧失和库存过剩。
With a single flexible and agile planning platform, Del Monte was able to integrate finance and supply chain planning processes, allowing its finance teams to accurately evaluate product costs and complete profitability analysis. The integration also empowered Del Monte to anticipate, predict, and accommodate market changes in real time. For example, because of El Nino, Del Monte struggled to prioritize product allocation. But now with Anaplan, they can run real-time scenarios and see what areas may not be profitable and report this back to their sales, channel sales, and logistic teams to adjust strategy.
\r\n\r\n
\r\n"}}" id="text-6497c677d2" class="cmp-text">
凭借一个灵活灵活的计划平台,德尔蒙特能够整合财务和供应链计划流程,使其财务团队能够准确评估产品成本并完成盈利能力分析。整合还使德尔蒙特能够实时预测、预测和适应市场变化。例如,由于厄尔尼诺现象,德尔蒙特公司很难对产品配置进行优先排序。但现在有了Anaplan,他们可以实时运行场景,了解哪些领域可能不赚钱,并将其反馈给销售、渠道销售和物流团队,以调整策略。
The supply chain finance planning process, which previously took two weeks, was narrowed down to two days using the Anaplan platform. Previously, when there were demand changes, it took Del Monte five days to react. With Anaplan, it now takes less than five minutes to come up with the necessary adjustments in its production. Del Monte can now look at what drives profitability of a channel, SKU, or customer on a monthly basis. Decision-makers now have visibility to this information, which arms them to make quick, informed decisions.
\r\n\r\n"}}" id="text-fa508b7011" class="cmp-text">
供应链金融规划过程以前需要两周时间,使用Anaplan平台后缩短到两天。此前,当需求发生变化时,德尔蒙特需要5天时间做出反应。有了Anaplan,现在只需不到五分钟就能在生产中做出必要的调整。德尔蒙特现在可以每月查看是什么推动了渠道、库存单位或客户的盈利能力。决策者现在可以看到这些信息,这使他们能够快速做出明智的决定。
Working in the fast-moving consumer goods industry, Del Monte’s products are time sensitive with a specific shelf life. Misalignment in supply and demand planning can have a direct impact on revenue. With another annual budgeting process quickly approaching, the speed to implementation became a deciding factor. While other vendors quoted a 9- to 12-month timeline, the implementation of the core supply chain finance model in Anaplan required only seven days of dedicated work, and less than two months of training, data integration, and requirements gathering.
\r\n"}}" id="text-5370b6ca7c" class="cmp-text">在快速消费品行业,德尔蒙特的产品对时间敏感,有特定的保质期。供应和需求规划的错位会对收入产生直接影响。随着另一个年度预算编制过程的迅速临近,执行速度成为一个决定性因素。虽然其他供应商给出了9到12个月的时间表,但在Anaplan中,核心供应链金融模型的实施只需要7天的专门工作,以及不到两个月的培训、数据集成和需求收集。
\r\nMy team handles the FP&A budgeting, forecasting, variance reporting. We had a system that was already conking out because of hardware issues. I didn’t want my team to go back to the Excel spreadsheets that we were using before. So we have three different workbooks for each channel. Each workbook has about 50 worksheets, and I approached my boss and said we need a platform for planning and for reporting.
\r\nWe work in the food and beverage industry and most of our products are in the fast-moving consumer goods segment, and added to that is the complexity that these products have shelf lives. If they don’t get delivered on time, or if they don’t get produced when the demand is there, wastage is very high. What we have implemented so far is the FP&A use case, and when I say FP&A, it’s the budgeting where we have volume and non-operating income. But at the same time we have embedded into that use case supply chain finance aspects. So that’s the logistics, warehouse capacity planning and soon the bill of material-based costing for our culinary products.
\r\nWith Anaplan, it’s really just like Excel on steroids. The multidimensionality of it, and then the fact that you can change your variable and everything automatically changes, it’s a big help for us because often times we have changes in the planning process where just key variables are being changed. When we were using BPC, if we had a variable change, we had to rewind the whole thing—so run volume allocation, run calculation because the changes were not dynamic and that’s where the productivity as well is coming from, from using Anaplan.
\r\nWe just completed the budget cycle, and obviously because of the El Nino phenomenon that we are facing and performance in the past, we have issues and we have to prioritize some of our product allocations. And now because we have Anaplan, when we run our first scenario, we saw that certain areas were not profitable and we went back right away to our sales people and our channel team and our logistics team to inform them about this mismatch—and right away they knew that they needed to adjust.
德尔蒙特是最大的菠萝产品生产商之一。我们提供了全球20%的菠萝供应。我们不只是卖菠萝,我们也卖健康和保健给每一个家庭。
我的团队负责FP&A预算,预测,方差报告。因为硬件问题,我们的系统已经瘫痪了。我不想让我的团队回到我们以前使用的Excel电子表格。每个频道都有三个不同的练习册。每个工作簿大约有50个工作表,我找到我的老板,说我们需要一个计划和报告的平台。
我们在食品和饮料行业工作,我们的大多数产品都属于快速消费品领域,除此之外,这些产品的保质期也很复杂。如果它们不能按时交付,或者在有需求的时候没有生产出来,浪费就会非常大。到目前为止,我们实现的是FP&A用例,当我说FP&A时,它是我们有数量和非营业收入的预算。但与此同时,我们已经在用例中嵌入了供应链金融方面的内容。这就是物流,仓库容量规划很快我们的烹饪产品的材料成本账单。
对于Anaplan来说,它就像是Excel的类固醇。它的多维性,事实上,你可以改变你的变量,一切都自动改变,这对我们来说是一个很大的帮助,因为我们经常在计划过程中有变化,只有关键变量被改变。当我们使用BPC时,如果我们有一个变量的变化,我们就必须倒带整个事情——运行容量分配,运行计算,因为这些变化不是动态的,这也是生产力的来源,来自使用Anaplan。
我们刚刚完成了预算周期,显然由于我们面临的厄尔尼诺现象和过去的表现,我们遇到了一些问题,我们必须优先考虑我们的一些产品分配。现在因为我们有了Anaplan,当我们运行第一个场景时,我们发现某些领域是不盈利的,我们立即回到我们的销售人员、渠道团队和物流团队,告诉他们这种不匹配,他们马上知道他们需要调整。
\r\nThe Anaplan platform integrated all planning processes, from the demand planning side to the distribution replenishment, to the production scheduling, all the way down to the material resource planning. Before, we were all doing this in separate processes and using legacy systems, with different Excel versions across all the processes.
\r\nIn managing our inventories across different various locations, there are usually disconnects; for example, the production planning processes don’t align with the deployment processes. Whenever there are misalignments in the planning process, it usually leads to lost sales opportunities or excess inventories.
\r\nAnaplan gave us speed and agility in reacting to all volatilities. I think that’s what we need nowadays, especially considering how fast our customer requirements are evolving.
\r\nIt used to take us five days to react to demand changes. Now, with Anaplan, it takes us less than five minutes to come up with the necessary adjustments in production.
\r\nIt also enabled collaboration across all the supply chain members, putting all key stakeholders under one platform and converging all efforts toward delivering the goods to our customers.
\r\nAnaplan brought us to the point where we can take our supply chain further in the future. It automated all our legacy processes, all our Excel spreadsheets, and brought us all together on one platform. It opened up lots of opportunities for us. And it enables us to do the transition for the future.
我是RK Del Rosario。我是德尔蒙特的供应链计划经理。
德尔蒙特拥有世界上最大的菠萝生产设施之一。它占世界菠萝产量的20%。
我们使用Anaplan管理270多种成品产品,800多种原材料和包装材料。全国有超过18个工厂。
ananplan平台集成了所有计划流程,从需求计划到分销补充,到生产调度,一直到材料资源计划。在此之前,我们都在单独的流程中使用遗留系统,在所有流程中使用不同的Excel版本。
在管理不同地点的库存时,通常会出现脱节;例如,生产计划流程与部署流程不一致。每当计划过程中出现偏差时,通常会导致销售机会的丧失或库存过剩。
anplan让我们能够快速和灵活地应对各种波动。我认为这就是我们现在所需要的,特别是考虑到我们的客户需求是如何快速变化的。
过去,我们需要5天时间来对需求变化做出反应。现在,使用Anaplan,我们只需不到五分钟就能在生产中提出必要的调整。
它还实现了供应链所有成员之间的协作,将所有关键利益相关者置于一个平台下,并将所有努力集中在向客户交付货物上。
Anaplan让我们在未来可以进一步发展我们的供应链。它自动化了我们所有的遗留流程,所有的Excel电子表格,并将我们都聚集在一个平台上。这为我们提供了很多机会。它使我们能够实现未来的转变。